Introduction: Why Transition from 2D to 3D?
For manufacturers, transitioning from 2D drafting to 3D modeling is not just a shift in tools—it's a transformation in how you innovate, design, and manufacture products. With the help of Autodesk solutions and KETIV’s expertise, companies are streamlining workflows, reducing errors, and accelerating time to market through automation and improved data management.
This comprehensive guide offers American manufacturers insights into best practices, real-world workflows, and actionable strategies to make the transition from a 2D drawing to a 3D model efficient and future-proof.
3D product design is the bare minimum to progressing as a digital manufacturer
The Difference in 2D vs. 3D Design
2D DESIGN | 3D DESIGN |
---|---|
Plane based 2-dimensional views to represent objects | Volume based 3-dimensional objects |
Sequential, linear design process | Iterative and flexible design process |
Interpretation required to understand multiple views | Comprehensive model that can be understood intuitively |
Error-prone when interpreting 2D drawings to physical parts | Validation features for checking interferences and issues |
Training required for traditional manufacturing | Knowledge of modern manufacturing technologies for CAM, NC, and Additive MFG |
The Benefits of Moving to 3D Design
- Enhanced Visualization
- Interactive Models
- Rapid Iteration
- Parametric Design
- Direct 2 MFG Capability
- Simulation and Analysis
- Real Time Feedback
- Reduced Development Cost
- Integrated Documentation
- Regulatory Compliance
- Complex Geometries
- Digital Twin
- Systems Integration
- Encourages Innovation
- Attractive to talent pool
- Opening up Automation
Laying the Foundation for Success
Planning Checklist: Five Key Steps for 2D to 3D Transition Planning
Transitioning from 2D to 3D design requires thorough preparation and a structured process. Below is a categorized checklist that outlines essential tasks and considerations to ensure a smooth transition, with definitions of how each supports the planning phase and long-term success.
1. Program Management and Leadership Alignment
Ensuring leadership buy-in and structured oversight keeps the transition on track and aligned with strategic goals.
- Assign a Program Manager: A dedicated manager will oversee timelines, resources, and stakeholder alignment.
- Identify Champions and Power Users: Appoint experienced users to lead adoption efforts and mentor others.
- Set Training Goals: Define the training strategy to ensure all team members will be able to gain proficiency with the new tools. (Example: Schedule basic and advanced Inventor or Vault training for different roles.)
- Initiate Internal User Groups: Facilitate collaboration across teams with recurring meetings or chat channels (e.g., MS Teams or Slack) to address issues in real-time.
2. Industry Research and Goal Setting
Research and benchmarks ensure you are following best practices and setting achievable goals.
- Research Industry Trends: Study how similar companies are leveraging 3D workflows to determine best-practices.
- Focus on Proven Methodologies: Adopt practices validated in similar industries to avoid common pitfalls.
- Identify Milestones: Set clear objectives to track the progress of your 3D adoption (e.g., first automated BOM release, first full 3D assembly).
- Measure Success: Define metrics for success, such as time savings, error reduction, or improved collaboration between teams.
- Anticipate Licensing Needs and Costs: Evaluate Autodesk tool licenses (e.g., Inventor, Vault, Plant 3D) and budget for future scaling.
3. Workflow Assessment and Cross-Functional Collaboration
Evaluate your current workflows and engage all stakeholders to ensure smooth integration.
- Assess Existing Workflows and Dependencies: Map current workflows across departments to identify manual steps or inefficiencies that can be automated. (Example: Identify manual BOM creation processes that can be automated with Inventor’s iLogic tools.)
- Engage Cross-Functional Teams: Ensure all relevant departments—engineering, operations, manufacturing, and sales—are involved in designing new processes. (Example: Align with sales on how BOMs will integrate into their order management systems.)
- Capture Design Standards and Templates: Document current design conventions, part naming schemes, and templates to maintain consistency across new 3D conversion workflows.
Want to take this list offline?
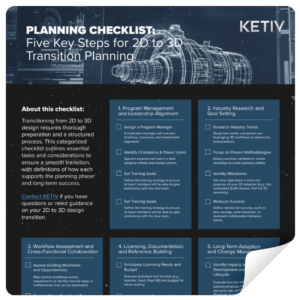
4. Documentation and Reference Building
Good documentation ensures continuity, knowledge sharing, and smooth onboarding of future team members.
- Maintain Good Documentation: Develop comprehensive documentation for new workflows, licensing processes, and troubleshooting guides.
- Build a Database of Reference Materials: Create a library of whitepapers, tutorials, and internal videos to support ongoing learning.(Example: Use Autodesk KVA recordings and unlisted YouTube tutorials to build this knowledge base.)
5. Long-Term Adoption and Change Management
Create a framework that ensures continuous learning, system improvements, and user engagement.
- Identify Impacts to Product Development and Customer Lifecycles: Evaluate how the transition will affect delivery timelines, customer expectations, and post-sale service processes. (Example: If manufacturing relies on 2D PDFs, ensure the new 3D process provides automated PDF exports through Vault.)
- Anticipate Team Size and Structure Needs: Plan for how many designers or engineers need to be trained, and whether dedicated resources are needed to manage data in Vault PDM.
- Plan for Recurring Engagement: Schedule monthly check-ins or team meetings to monitor the transition and identify areas for improvement.
File Organization
Transitioning to 3D parametric design generates a large volume of data, including Inventor project files, 3D models, 2D drawings, Revit outputs, simplified models, iParts, and specifications. Managing these efficiently goes beyond basic Windows Explorer; a Product Data Management (PDM) system like Autodesk Vault is essential. Vault allows you to organize files with searchable properties, eliminating the need for deep folder structures while ensuring easy access and version control across teams.
Naming Conventions
Unique and consistent file names are essential for efficient data management. Descriptive or alphanumeric names can provide quick context, while smart numbering ensures logical organization. Some teams may prefer sequential arbitrary names, but adopting a PDM-provided naming scheme like Autodesk Vault’s ensures consistency and reduces errors. Thoughtful naming makes files, such as 2d CAD drawings or 3D renderings, easier to search, manage, and integrate into automated workflows.
Optimizing Data Flow Between Teams
Understanding how engineering interacts with product and project data is essential for smooth operations. Key considerations include the data provided by sales, the systems used to deliver that data, and how engineering integrates information from external sources. It's also important to assess the formats of incoming data and whether engineers can access it quickly. Streamlining this data flow ensures timely decision-making and reduces project bottlenecks.
Effective Metadata Management
Metadata plays a crucial role in enhancing the value and accessibility of engineering data. By assigning detailed characteristics to files, it improves searchability and ensures data compliance across systems. Well-structured metadata allows for better classification, supports IP preservation, and makes data more useful for downstream processes. This increased visibility enhances user experience, ensuring teams can trust the data's legitimacy and leverage it efficiently across the organization.
Preparing Autodesk Inventor + Vault for 3D Content: Tools, Libraries, and Standards
Successfully shifting from 2D drafting to 3D design requires more than just new software—it demands a well-structured approach to workflows, documentation, and data management. This portion of the guide outlines best practices to assess your current state, establish design standards, and streamline the transition to 3D. By reviewing workflows, documenting standards, and implementing consistent naming conventions, teams can avoid rework and ensure smooth collaboration.
Preparing the Models
Review Your “As-Is” State
Understanding where you stand today helps shape your path to 3D design. Document your existing workflows and assess frequently used 2D drawings. This creates a baseline for identifying inefficiencies and aligning current practices with your future 3D process.
Catalog all essential drawings and ensure your workflows are well-documented—not just how files are created but how they move through different departments. As Greston Dunivan noted, “Understanding the flow of work ensures smooth transitions and avoids rework.”
Capture documentation standards that apply to all designs and drawings:
- Line Styles & Dimensions: Ensure clarity and uniformity in all design outputs.
- Business-Related Properties: Standardize part numbers, stock numbers, and descriptions to streamline product tracking and BOM creation.
Establish Standards for Design Consistency
Clear standards help maintain alignment between design and manufacturing:
- Measurement Standards: Use consistent units across projects (e.g., inches or millimeters) to avoid manufacturing errors.
- Naming Conventions: Develop unique, alphanumeric naming schemes for parts and assemblies to prevent duplication and confusion.
- Dynamic or Static Data: Identify which components will remain static and which will require parametric adjustments. This ensures efficient design and reuse without unnecessary duplication.
Define Modeling Standards
Achieving a seamless transition from 2D to 3D requires consistency across modeling practices. A structured approach ensures your team works efficiently and reduces rework. Below are key elements for maintaining uniformity during the transition:
Usage of Origins
Aligning parts using consistent origin planes helps maintain uniformity when constraining assemblies. This makes it easier to insert components into shared assemblies with predictable behavior.
Modeling Tools & Techniques
Establish clear guidelines for the use of essential modeling tools to ensure consistency:
- Sketching: Standardize sketching practices to avoid discrepancies when creating initial designs.
- Extrusions: Use extrusions as the primary method to shape 3D parts, ensuring familiarity and ease of use.
- Holes: Develop team-wide standards on whether to use circles or center points for holes to minimize variation in designs.
Creating and Managing Assemblies
Consistent assembly practices help ensure designs are easy to modify and share across teams.
- Constraints: Agree on how to apply constraints within assemblies to keep components properly aligned.
- Orientation: Establish rules for part orientation within assemblies, ensuring uniformity across different projects.
- Design Views: Utilize design views to improve efficiency and ensure that teams can easily interpret complex assemblies.
By focusing on these aspects, you’ll set a strong foundation for your transition to 3D, ensuring your team works efficiently and maintains a high level of accuracy across designs. As Greston Dunivan from KETIV noted, having consistency within these elements ensures team members can pick up and modify others’ work seamlessly.
Define Drawing Standards
When transitioning to 3D, aligning design practices with fabrication intent ensures manufacturing teams can efficiently interpret and use your drawings. Below are essential strategies to optimize drawing methodologies and leverage advanced capabilities:
Defining Drawing Methodology
Establishing a consistent drawing structure ensures clarity and accuracy for production teams:
- One Part / One Drawing: Create individual drawings for each part to simplify communication and avoid confusion.
- General Arrangements: Use high-level assembly drawings to show how components fit together.
- Detail Views: Include zoomed-in views for complex components to provide specific manufacturing instructions.
Leveraging Parametric Views for Efficiency
3D modeling allows for more advanced drawing views and capabilities than 2D:
- Filtered Bill of Materials (BOM): Automatically generate BOMs specific to each drawing, showing only relevant components for subassemblies.
- Hidden Lines: Display hidden lines automatically to provide deeper insights into complex assemblies.
- Detail Pages: Add additional pages to show intricate parts and structural details without cluttering the main drawing.
Utilize the advantages of 3D to deliver clearer and more actionable information to production teams. With parametric views and dynamic drawings, teams can quickly extract the information needed for manufacturing without manual rework. As Greston emphasizes in the video, “The more detail, the better.” Providing detailed, well-structured drawings reduces shop floor confusion and minimizes interruptions during production.
Define Properties Standards
Strategic management of critical properties ensures consistency, clarity, and efficiency throughout the design and production process. Thoughtful planning of property management will streamline the workflow, improve data accuracy, and simplify downstream processes.
Capture Critical Properties
Collecting essential attributes helps ensure that parts and models are properly tracked and integrated into broader systems, such as ERP or BOMs:
- Part Numbers: Assign unique identifiers to avoid duplication and ensure traceability.
- Stock Numbers: Manage inventory and track availability accurately within production systems.
- Descriptions: Provide concise yet descriptive information for easier reference across teams.
Leverage Parametric Values and Formulas
Using parametric models ensures flexibility and efficiency:
- Parametric Values: Capture key properties directly in the models to automate changes across drawings and assemblies.
- Parametric Formulas: Use embedded formulas to auto-populate properties like dimensions, part numbers, or custom fields. This eliminates repetitive work and reduces errors.
Define Parts and Standardize Naming Conventions
Clear part definitions ensure that every component fits seamlessly into the overall design and assembly process. Consistent naming and definitions help teams work more efficiently, especially when dealing with dynamic or configurable parts.
By leveraging parametric values and formulas, engineers can dynamically adjust designs without starting from scratch, saving valuable time. As emphasized during the session, “Use properties wherever you can. They’re not just for organization—they ensure that all the right data flows seamlessly downstream, from BOMs to ERP packages.”
Develop Templates Libraries
Templates and the content center ensure consistency, accuracy, and efficiency by standardizing designs and simplifying the reuse of parts and assemblies.
Provide a Single Starting Point for Engineers
Templates help engineers jump right into projects by offering predefined models, drawings, and assemblies:
- Simple Parts: Standard parts with embedded properties, ready for immediate use.
- Complex Assemblies: Pre-configured assemblies that can be modified to fit specific project needs.
- Drawing Pages or Packages: Templates for individual drawings or complete drawing sets, ensuring layout consistency.
Establish Standards for Designs
Standardization ensures alignment across engineering teams and downstream processes:
- Business-Related Properties: Templates include essential properties like part numbers, stock numbers, and descriptions to streamline data management.
- Measurement Standards: Define units (e.g., inches, millimeters) and tolerances to maintain accuracy throughout designs.
- Naming Conventions: Ensure consistency by applying naming rules to parts and assemblies, making them easy to find and track.
Develop Content Center Libraries
Leverage Content Centers for Reusable Components
Content centers contain preloaded standard parts (e.g., bolts, pipes) and templates for frequently used assemblies, providing a centralized library. As mentioned in the clip, content centers are “completely independent of other tools like Vault, ensuring that everyone pulls from the same source for reliable, consistent design.”
By using templates and content centers, engineers can minimize repetitive work, reduce errors, and ensure alignment between teams. This structured starting point simplifies the creation of both simple and complex designs, helping engineers focus on innovation instead of administration.
Expanded Standard Parts
Vault’s Content Center provides a vast library of preloaded components containing thousands of standard screws, bolts, nuts, washers, pins, and more, that can be inserted in assemblies:
- Extreme Configurability: Modify parts to fit specific design needs (e.g., adjust bolt lengths, pipe materials).
- Contains a Large Set of Standard Parts: Access thousands of structural components, bolts, and fittings.
- Best Utilized for Configurable Parts: Ideal for parts that require multiple size or material variations.
- Accommodates Purchased or Designed Parts: Store both off-the-shelf components and internally designed elements.
Populating Parts with Key Standards
The flexibility of content centers ensures that parts are enriched with critical information, making them ready for use across teams:
- Business-Related Properties: Store essential data such as part numbers and descriptions for seamless integration with BOMs and ERP systems.
- Measurement Standards: Standardize units, tolerances, and dimensions to ensure accuracy across different projects.
- Naming Conventions: Consistent naming reduces redundancy and simplifies searches, ensuring the right parts are used every time.
Content centers, as emphasized in the webinar, “are completely independent from other systems like Vault, ensuring every engineer pulls from the same source.” By configuring and populating these libraries with relevant data, teams can minimize rework, improve accuracy, and align better with business processes.
Data Management: Releases and Revisions
Robust data management ensures your design process remains efficient, organized, and secure. A well-defined process for releases and revisions improves communication across teams, protects intellectual property, and ensures that changes are accurately tracked.
Define Your Process and Improve Communication
To successfully manage data:
- Establish Clear Processes: Map out your release and revision workflows to avoid bottlenecks and ensure every stakeholder understands their role.
- Focus on Communication: Share updates across engineering, manufacturing, and operations teams to align activities and avoid duplication.
- Share Information Effectively: Ensure that updated files, BOMs, and drawings reach the right people on time to prevent delays.
Leverage Your PDM for Tracking and Security
A Product Data Management (PDM) system like Autodesk Vault can help teams organize and safeguard design data:
- Track Drawing and BOM Revisions: Use PDM tools to monitor every change, ensuring nothing is lost or overwritten.
- Protect Intellectual Property: Securely store and control access to sensitive design files, ensuring only authorized personnel can modify or access them.
- Utilize Distinct Release Workflows: Implement workflows that differentiate between initial releases, updates, and special approvals, streamlining complex product lifecycles.
As shared in the webinar: “Defining workflows for releases and revisions is critical for ensuring smooth communication between departments and avoiding manual errors.” With the right data management practices, teams can stay aligned, reduce errors, and maintain a clear history of every design change, leading to better outcomes for both engineering and production.
Streamlining with Design Automation
Getting Started with an Example of Design Automation
Design automation through iLogic in Autodesk Inventor enables you to eliminate repetitive tasks and ensure product consistency. In the webinar session listed in this section, Javier Chavez demonstrated a tank configuration workflow where automation allows users to adjust dimensions and generate assemblies on the fly.
Benefits of Design Automation
- Dynamic Configurations: Automatically adjust subassemblies based on product variations.
- Error Reduction: Automation ensures that constraints and relationships within assemblies are accurate.
- Improved Time to Market: Generate designs, drawings, and BOMs in minutes instead of hours.
Tank Assembly Example
A tank manufacturer can configure assemblies by selecting size, inlet types, and other components from a dropdown menu in an iLogic-driven dialogue box. With a few clicks, the tool generates the correct 3D assembly, naming convention, and associated BOM—all automatically stored in Vault PDM.
Note: You can work with this very same use case if you download our Automation Starter Kit.
Get started with Design Automation in iLogic
This DIY Automation Kit allows you to experiment with iLogic-based workflows. Watch the video and down the kit so you can follow along with the same files.
Managing Design Workflows and Data
Audit Your Current Data & Workflows
Transitioning from 2D to 3D workflows requires a comprehensive understanding of your current process. Begin by documenting key outcomes, dependencies, and how your data flows across teams and departments.
- Identify Key Data Needs: Pinpoint what data is essential at each stage of your design and manufacturing processes. Consider information needed from upstream departments, like sales, as well as the data required to support downstream needs, such as production or vendor communications.
- Assign Data Ownership: Define who is responsible for data accuracy and updates at every step. With a clearer understanding of accountability, it’s easier to maintain quality control and streamline workflows.
- Manage Process Streams by Product: Multiple product lines may require distinct workflows, each with unique data requirements and transformation points. Charting out these process streams helps to identify and prioritize improvements that will enhance efficiency across varied product types.
- Track Data Transformation Requirements: Determine how data must change or adapt throughout its lifecycle. For instance, raw CAD data may need to be translated into neutral formats or BOMs to be useful for engineering or production.
- Preserve and Secure Data: Throughout this process, ensure that data is stored in secure, accessible locations where it can be accurately maintained and easily retrieved.
Capture Engineering Data Inputs and Outputs
For a smooth transition to 3D workflows, it’s crucial to clarify the inputs and outputs that guide engineering teams. Understanding how data flows into and out of engineering helps prevent errors and ensures alignment across departments.
- Define Engineering Triggers: Identify how engineering knows what to produce. Collaborate with Sales to determine the initial data that guides engineering, including specifications, job numbers, and essential project details.
- Integrate Sales and Engineering Systems: Evaluate the systems that Sales uses to communicate with Engineering. Streamlined data-sharing tools and consistent workflows between departments prevent miscommunication and ensure engineering starts each project with accurate, relevant information.
- Evaluate Data Consistency: Determine the consistency of data inputs. With reliable, well-structured data from Sales, engineering can reduce rework and focus on design and development instead of troubleshooting inaccuracies.
- Clarify Manufacturing Needs: Understand what data formats and levels of detail are necessary for Manufacturing. This includes specific file types, BOMs, and drawings that can seamlessly integrate into production workflows.
- Identify Vendor Data Requirements: If external vendors rely on your data for accurate production, ensure they have access to the appropriate file formats and information, reducing back-and-forth and speeding up delivery timelines.
Identifying Downstream Dependencies
Ensuring that engineering data flows efficiently to downstream processes is vital for maintaining smooth operations from design to production.
- Data Dissemination to Manufacturing: Clarify how engineering data is shared with manufacturing. Establish a streamlined method for sending finalized drawings, BOMs, and specifications directly to production, reducing delays and enhancing accuracy.
- Understanding Data Consumption: Examine how manufacturing consumes this data. Knowing which formats and data points production relies on allows engineering to tailor outputs, making them more accessible and useful.
- Facilitating Downstream Processes: Engineering can play a proactive role in supporting downstream tasks. By anticipating manufacturing’s data needs and aligning outputs accordingly, engineering can reduce misinterpretation and simplify workflows.
- Raw vs. Processed Data: Determine whether raw engineering data is suitable for production use or if further processing is necessary. If transformation is required, incorporate this as a standard step to ensure consistency and usability across departments.
Considering People, Roles, and Responsibilities
Transitioning to a 3D environment involves more than just technology—it requires a team aligned with well-defined roles to drive the process smoothly and effectively.
- Leveraging Skillsets: Identify team members with specialized skills who can actively contribute to the 3D transition. Consider the unique strengths of each individual, whether they’re experts in design, automation, or data management.
- Talent Pool: Tap into a diverse group of skilled professionals to support various aspects of the transition. This pool can include experienced designers, engineers, and IT staff familiar with system integrations and workflows.
- Internal Champions and Power Users: Establish “champions” who can advocate for and lead the 3D adoption efforts. These power users will provide valuable insights, promote best practices, and help train colleagues, ensuring consistent application of standards.
- Data Validators: Assign dedicated staff to review and validate data for accuracy before it’s distributed. By ensuring data integrity early on, these validators help prevent downstream errors and rework.
- Release Managers: Release managers play a key role in coordinating the timing and sequence of data releases, making sure that all dependencies are accounted for and that files are correctly routed to the next stage in the process.
- Document Control & Administration: Create or designate a role for maintaining document control, including managing libraries and organizing content to support consistent data use. Librarians or admin staff ensure that standards are met, files are accessible, and data remains organized across projects.
Re-Using Existing 2D Models
When to Re-Use Existing 2D Data:
- Static Parts or Components: Parts that don’t undergo frequent changes are ideal for reuse. These components are often core elements of larger assemblies and can be reliably carried over into 3D.
- Simple Designs: Straightforward parts or assemblies, especially those with minimal detail, are well-suited for reuse as they transition more easily into 3D.
- Library Components: Common parts, such as bolts, nuts, or base structures, which are repeatedly used across different projects, can become part of a 3D library for easy access and consistency.
Leveraging existing 2D models as a foundation for 3D design can streamline the transition, especially when the models meet certain criteria. Here’s a guide for when it makes sense to reuse 2D data and when it’s best to start fresh.
When Not to Re-Use:
- Complex Designs: Intricate models with detailed geometry are often better rebuilt in 3D from scratch to ensure optimal detail, functionality, and customization.
- Designs Prone to Change: If a component frequently updates, it’s often more efficient to create a dynamic 3D model that accommodates these changes.
- Automation-Ready Models: For parts intended for automation, re-using 2D models can create limitations. Freshly built 3D models allow for parametric adjustments, making them a better fit for automated processes.
Careful consideration of the model’s purpose and complexity will help determine when reusing 2D models can benefit the workflow and when it’s best to develop new 3D models.
Re-Using Existing 3D Models
Re-using 3D models offers significant efficiency gains when transitioning from 2D to 3D conversion. The following guidelines outline when re-use is beneficial, and when creating new models may be preferable.
When to Re-Use 3D Models
- Stable, Static Parts or Components: Parts that don’t change frequently, such as base components or widely-used elements, are ideal candidates for re-use. They add consistency and streamline larger assemblies without needing updates.
- Purchased Components: Vendor-supplied parts, like fasteners or electrical components, are excellent for reuse. These can be quickly sourced and integrated across different projects.
- Library Components: Utilizing a central library for common parts saves time and ensures standardized usage throughout projects. Autodesk Inventor’s Content Center Libraries provide over 750,000 parts, with options to customize and adapt components as needed.
When New Models are Better
- Designs Prone to Frequent Change: For components that need regular updates or variations, creating new models enables flexibility, avoiding the constraints of re-used designs.
- Automation-Ready Models: Re-used models may lack the parametric features needed for automation. If automation is part of the workflow, purpose-built 3D models configured for adaptability are essential.
Importing and Simplifying Models
Imported models from suppliers or online libraries can include excessive detail, slowing down workflows. Simplification helps reduce file sizes while retaining essential features:
- Data Formats: Import neutral formats like STEP, IGES, STL, or OBJ, and native formats such as SolidWorks, Creo, or Catia.
- Simplification Process: Upon import, simplify the geometry to retain only critical details. File size reductions of up to 95% are achievable, reducing files from 42MB to under 214KB, boosting performance without sacrificing necessary data.
Incorporating these guidelines helps strike a balance between speed and customization, creating a streamlined workflow that leverages re-use, automation, and efficient data management.
Comprehensive Data Management with Autodesk Vault
Why Vault PDM Matters
Managing increasing volumes of 3D CAD model data is a critical challenge. Autodesk Vault PDM provides a centralized platform to manage revisions, control file access, and automate release processes.
- Centralized Repository: Store drawings, 3D models, and BOMs in a secure environment.
- Automated Release Workflows: Generate PDFs or DXFs and distribute them automatically when files are released.
- Revision Control: Track every version of a part or assembly to ensure team members access the latest
Efficient data management is crucial as companies transition from 2D to 3D design. Autodesk Vault provides a centralized, secure environment that streamlines data handling, ensuring engineering teams can manage complex workflows and protect intellectual property.
- Centralized Data Storage: Autodesk Vault offers a secure, single-source repository, eliminating the risk of data loss or unauthorized access. This platform ensures your files are consistently accessible and safeguarded.
- Robust Security Controls: Vault’s role-based permissions secure data at multiple levels—file, folder, and category—so users only access what they need. Folder and file-based security settings reinforce Vault’s position as a secure environment, particularly valuable for sensitive engineering information.
- Lifecycle and Revision Management: Manage the complete lifecycle of your files, from design creation to release and beyond. Vault’s lifecycle management tools provide version control, detailed revision tracking, and ensure that all stakeholders are working with up-to-date information.
- Broad Compatibility and Integration: Vault integrates with numerous Autodesk and non-Autodesk software tools, allowing seamless data flow across platforms. This compatibility enables engineers to pull data from other CAD systems and facilitate cross-department collaboration.
- Automation and Integration: With built-in automation tools, Vault can streamline tasks like BOM updates and automatic file exports (PDFs, STEP files, etc.), enhancing efficiency across the engineering and manufacturing process.
Implementing Autodesk Vault enhances collaboration, controls data consistency, and prepares your team to handle the increased data demands of 3D design, supporting productivity and security from concept through production.
💡 Example: Vault PDM can automatically export BOMs and PDFs to ERP systems when files are released. This eliminates the need for manual handovers and reduces errors.
🔗 Learn More: Vault Data Management
Automating and Integrating Key Manufacturing Systems
Effective revision control ensures seamless collaboration and prevents data loss or errors across engineering workflows. Managing complex product data demands robust tools and automated processes to track and publish changes efficiently.
Automated Publishing
Leverage automated workflows to generate PDFs during part release, ensuring the shop floor gets accurate documentation, saving time and minimizing errors. These tools handle:
- PDFs, STEP, DXF files: Automatically generated upon release to meet documentation and manufacturing needs.
- BOMs: Dynamic bills of materials that stay updated with every design change.
Managing BOMs and Items
Revision control isn’t just about drawings—it extends to items and BOMs. Organized items allow engineers to structure data effectively, while BOMs ensure the correct parts are used downstream. With integrated item management, data stays consistent and accessible. You can also trigger automatic export of BOMs to ERP, reducing manual entry errors.
Data Standards Compliance
Implement data standards to ensure quality and consistency across files. This includes naming conventions, property management, and controlled access to avoid duplication or unauthorized changes.
ERP Integration with KETIV DataBridge
The KETIV DataBridge facilitates smooth ERP integration, linking engineering data with business systems:
- Part and BOM Release: Automatically send released parts and BOMs to the ERP system for production.
- Item Master Retrieval: Seamlessly pull item master data from the ERP into engineering workflows.
- Workflow Process Triggers: Define triggers that initiate downstream actions—such as generating PDFs or updating BOMs—upon data release.
FAQ: Common Questions About 2D to 3D Transition
Yes, AutoCAD remains essential for schematics, piping diagrams, and other 2D sketch workflows.
Begin with small automation tasks using iLogic. Templates and libraries are a great place to start automating repetitive processes.
Vault ensures version control and manages user permissions, keeping your intellectual property secure.