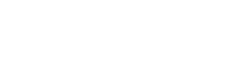
Traditional testing is a time-to-market killer
Time-consuming and costly testing
Physical tests slow down product development, delaying time to market and risking competitive advantage.
Late discovery of flaws
Identifying defects late in the product development process leads to costly rework, with expenses rising the further along you are.
Uncertainty and unreliability
Physical testing alone can’t guarantee long-term durability, leaving room for critical product failures and upset customers.
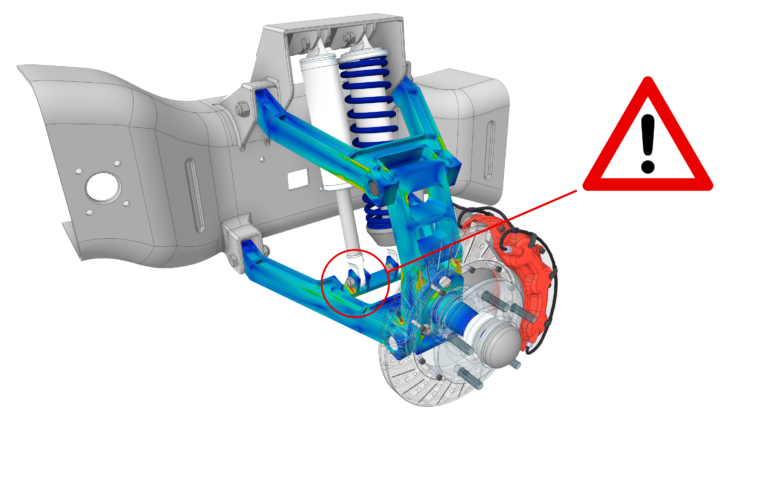
Accelerate your new product development process while boosting quality
Market-acceleration
Faster and fewer design cycles that minimize or eliminate the need for real-world testing.
“Being able to model something, run it in Ansys, and get results in a day or even a few days has allowed us to cut down turnaround times from 6 months or a year to just weeks—or even days.”
System-level analysis with multiphysics
The only solution allowing simulation of an entire system and across the different environments your product will need to endure.
“With Twin Builder, we have a platform offering many different Ansys software solutions with possible scalability for the future. If we want to take a deeper look into the multiphysics simulation of our electric powertrain technology, Twin Builder makes that possible.”
Martin Füchtner, Technical Project Leader for Formula E at Porsche Motorsport
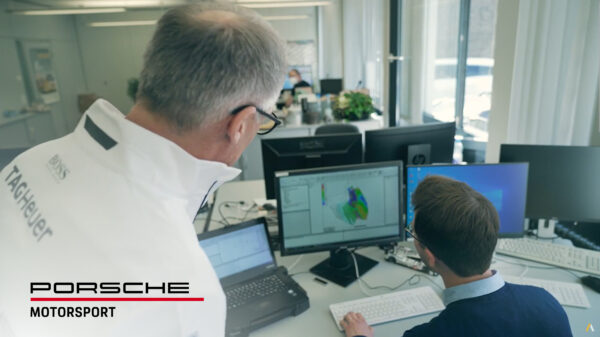
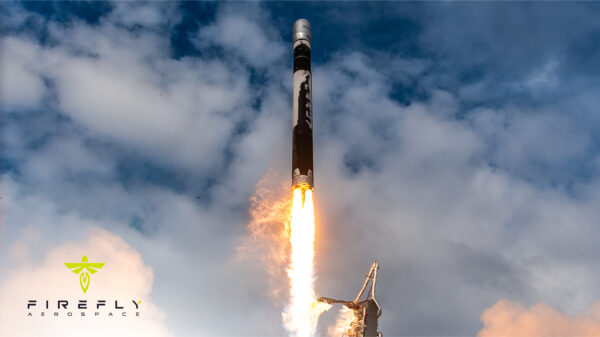
Optimize quality and performance
Come up with the most optimal approach, first. Discover weak points in a design and overcome them before they are prototyped.
“Leveraging the suite of Ansys tools allows us to ensure a design works with limited test iterations, providing up to $5 million in cost savings in engine cooling design, $10 million in increasing engine thrust and up to $500,000 in mass optimizations.”
Simulation Download
Engineering Smarter Connected Products for Winning in the Digital Economy
KETIV — Your Innovation Partner
Best-in-class simulation with a deeper tool set
KETIV is dedicated to finding the best simulation solution for you—whether it’s Autodesk Nastran for fundamental structural simulations, Ansys for advanced CFD analysis, or specialized consulting for a one-time project.
Why choose KETIV
- Unbiased Guidance: We focus on your needs, not on pushing a particular technology.
- Tailored Solutions & Support: From consulting, to support and enablement, we help you find the right simulation tools and strategies to bring your vision to life.
- Depth of Offerings: More than just simulation, KETIV also prides itself on a deep bench of experts and solutions in data management (PDM/PLM), sales automation (CPQ), design automation, and system integration.
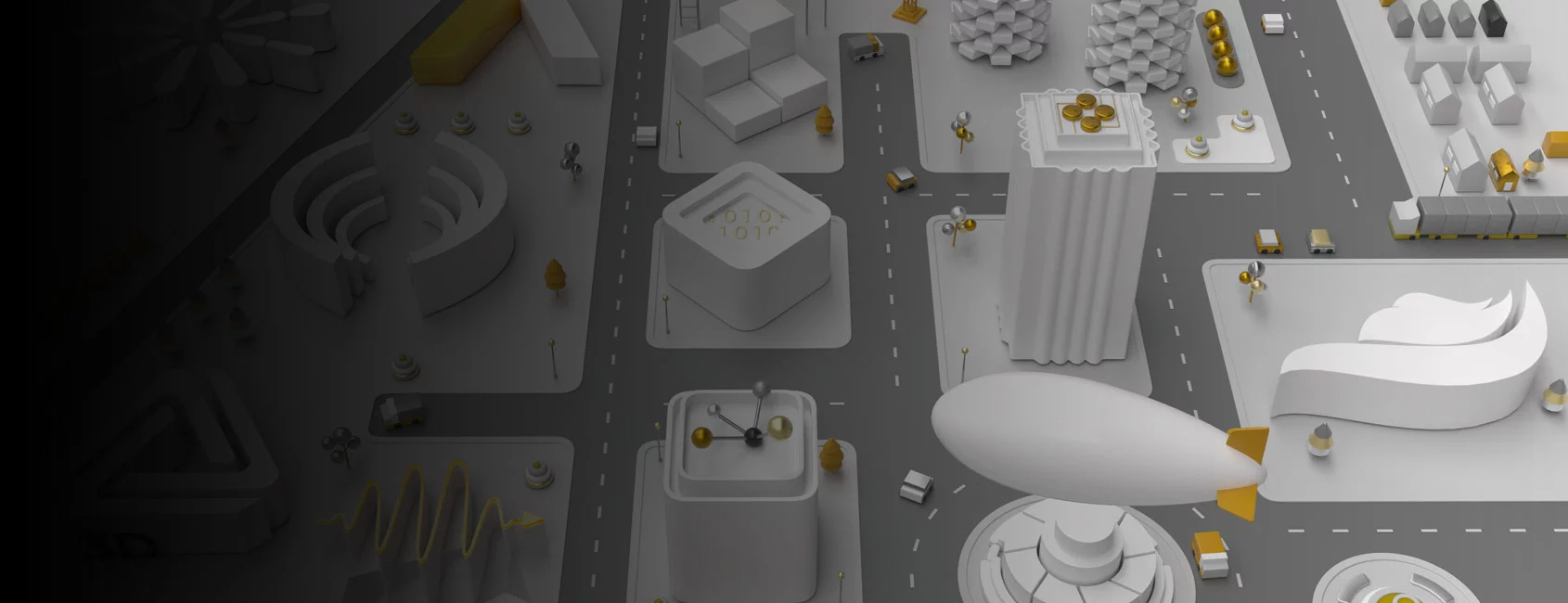
Engineering Smarter Connected Products for Winning in the Digital Economy
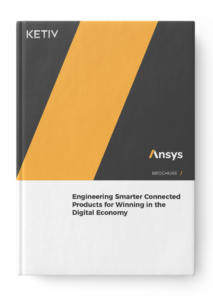
Together, We Can Achieve More
Join others who’ve turned vision into reality.
You’re not alone on this journey. Many innovators have partnered with KETIV to overcome challenges and achieve remarkable results.
We know that embracing new technology can be daunting. That’s why KETIV is here to support you at every turn. With resources like the KETIV Virtual Academy (KVA) and our dedicated team, we ensure you’re never alone on your path to success.
Because when you succeed, it’s not just a win for you—it’s a win for everyone who believes in pushing boundaries and achieving greatness.
Ready to create something exceptional?
More simulation stories
Simulation FAQs
Embarking on a new journey can bring up many questions. That’s why we’ve gathered answers to the most common inquiries about simulation in our FAQ section.
Mechanical software simulation is a powerful simulation tool that forecasts the effects of diverse loading conditions on products and production systems. Today, this process is chiefly executed through advanced finite element analysis software, which streamlines the mathematical workload for design engineers. Consequently, engineers can tackle more complex challenges that transcend the boundaries of manual calculations.
FEA originated as a method of stress analysis in the design of aircraft. Today it’s used across various industries, from civil engineering (for analyzing things like beams, plates, and foundations) to ship-building, motor, and engine design.
FEA predicts what will happen to a product under a range of conditions, providing valuable insights for design optimization. It does so by breaking a physical object down mathematically into thousands of tiny elements and using algebraic formulations to calculate how each one will respond. By synthesizing the behavior of these interconnected elements, a comprehensive perspective emerges, revealing the overall impact of physical forces on product behavior.
There are many different ways to tackle mechanical simulation, each aimed at handling particular engineering issues and goals. These approaches include stress, thermal, impact, and durability analyses.
Stress analysis predicts how a component or assembly could fail under loading conditions, such as bending, tension, compression, shear, and torsion. It considers factors such as geometry, material properties, and boundary conditions set by the engineer.
There are two main types of stress analysis: static and dynamic. A static load changes slowly, while a dynamic load happens fast. Dynamic loads, which include the movement of people, wind, waves, traffic, snow, earthquakes, and blasts, are less predictable and, therefore, require more complex simulations.
Thermal analysis predicts how the physical and chemical properties of components, products, or systems will behave when subject to changes in temperature. The results determine the thermal stability of materials, thermal expansion, and their ability to conduct heat.
Thermal analysis is an umbrella term covering multiple methods and techniques, including:
- Differential Thermal Analysis (DTA): The measurement of temperature differences between a sample and reference material when subjected to different temperatures.
- Differential Scanning Calorimetry (DSC): The determination of heat flow differences between a sample and reference material when subjected to different temperatures.
- Thermogravimetric Analysis (TGA): The analysis of mass changes in a material when subjected to different temperatures.
- Thermal Mechanical Analysis (TMA): The analysis of dimensional changes in a material, such as expansion or contraction, when subjected to different temperatures.
Impact analysis forecasts the response of a material or structure to an impact or collision event. It is widely employed by automakers when evaluating the crash-worthiness of new car models.
Engineers in the automotive industry need to understand the energy thresholds cars can endure before experiencing plastic deformation. Additionally, they need to ensure these vehicles meet stringent legal safety regulations. While physical tests can be costly and limited in scope, computer simulations offer a comprehensive and precise alternative for assessing impact resistance.
Durability analysis predicts when a component or structure will fail due to fatigue. The ultimate goal is to ensure that products can withstand the rigors of daily use and have a longer service life, improving customer satisfaction.
This sophisticated technology is extensively employed in the design and development of automobiles, aircraft, and heavy machinery, where the integrity of crucial elements such as spot welds and long-lasting seam welds is imperative to prevent fatigue-induced failures. It also enables the prediction of composite material performance, fostering the creation of lightweight and resilient products.
Fluid simulation models the behavior of fluids, such as air, water, and oil, as they flow through products or systems. It is particularly useful for projects involving complex fluid dynamics, such as the combustion of gases in automobile engines, airflow through jet engine turbines, and heat transfer among components on printed circuit boards.
Spanning diverse industries and fields, fluid simulation techniques like Conjugate Heat Transfer (CHT), Multiphase Flows, Reacting Flows, and Fluid-Structure Interaction (FSI) provide invaluable insights for performance optimization.
- Conjugate Heat Transfer (CHT): Simulates heat transfer between fluids and solids.
- Multiphase Flows: Can be used to model mixing, separation, mass transfer between two or more phases.
- Reacting Flows: Can predict product concentrations in the domain after species undergo reactions such as in combustion or electrochemistry.
- Fluid-Structure Interaction (FSI): Simulates the interaction between fluids and structures.
Electronics simulation models how an electronic device, component, or circuit performs under various conditions, including input signals, component values, and operating environments. This simulation model can be subdivided broadly into three categories:
- Analog Simulations: Focus on continuous-time, continuous-value signals, and systems.
- Digital Simulations: Focus on discrete-time, discrete-value signals, and digital systems.
- Mixed-Mode Simulations: Combine both techniques to analyze mixed-signal circuits that contain both analog and digital components.
Simulating a circuit’s behavior before construction can significantly improve design efficiency, enabling engineers to detect and address flaws early in development. Simulation is particularly beneficial for modeling integrated circuits, where tooling is expensive and impractical and testing internal systems is challenging. Power integrity, EMI/EMC, and signal integrity analysis can guard against fluctuating input voltages, electromagnetic interference or emissions, and crosstalk.
Electromagnetic simulations model the performance of the electromagnetic components of a device in both low and high frequency domains, by allowing visualization of electromagnetic fields. These types of simulation can encompass:
- Low-Frequency Electromagnetic Simulations: Permanent magnets, electromagnets, coils, motor/generators, actuators, sensors, transformers, wireless charging.
- High-Frequency Electromagnetic Simulations: Antenna performance, RF, microwave, filters, transmission lines.
Simultaneous simulation of both electromagnetic and electronic device operation provides more comprehensive benefits and faster development times. Note as well that electromagnetic and electronic simulations can be conducted at varying scales—from the microchip level, to packaging, PCB board, component, sub-component, and the whole system level—such as a battleship or a city. At an even larger scale, the whole system for space applications can include satellites in orbit around the earth and their ground stations.
Optics simulation allows you to accurately and robustly simulate your optical and optically enabled products. Conduct precise analysis, optimization, and tolerancing of your systems to ensure that these systems are designed for manufacture and can be built at scale with tested enhanced functionality and brought to market quickly. Leverage physics-based light simulation to understand how your products look under real-world lighting and usage conditions, to visualize future products.
Optical simulation can simulate the propagation of light through optical and optically enabled products from the nano- to the macro-level, allowing for integrated modeling and co-simulation that enables the accurate and robust design of such products. It includes these capabilities:
- Ray Tracing: Sequential or nonsequential ray tracing can be used to simulate light propagation through your optical systems.
- Perceived Visual Appearance: Human and other sensors can simulate what you or a camera will see prior to prototyping.
- Structural, Thermal, and Optical Performance (STOP) Analysis: The impact of structural deformation or thermal fluctuations on optical performance can be accounted for.
- Design for Manufacturability: The impact of manufacturing tolerances on a design can be simulated and compensated for, prior to production.
- Photonic Simulation: Nano-scale photonic components, circuits, and systems can be simulated to enable novel optical capabilities.
Sounds elicit strong emotions that can add or detract significantly from a product’s user experience. One engineering error that leads to poor sound quality can render an otherwise perfectly designed product unusable.
Vibration and acoustic simulation help prevent such slip-ups from happening. These tools allow engineers to foresee how structures and systems react to vibrational forces and sound waves, ensuring the final product strikes a harmonious balance between top-notch functionality and crystal-clear acoustics.
Whether examining an electric vehicle (EV), turbine, or home speaker system, engineering simulation software empowers you to uncover a range of acoustic characteristics without creating a single physical prototype. Below are some examples:
- Assessing and Refining Sound Quality: Seamlessly integrate acoustic simulations with empirical data from laboratory tests to meticulously analyze and refine sound quality across a diverse array of products.
- Enhancing Engine Acoustics: Elevate electric and traditional motor design by audibly experiencing the acoustics of the motor and its sub-components at various speeds. Using simulation data to minimize noise and vibration creates a more immersive, enjoyable, and secure driving experience.
- Rendering Component-to-System Sound: Immerse yourself in the auditory experience of your product and its individual components in true-to-life settings, simulating daily usage to ensure optimal performance.
Many of the above simulations depend on accurate materials data to obtain accurate simulation results. Material and process choices—for example, the use of rare earths in magnet design—can dictate availability and cost with simulation results. A known-good repository of materials data makes selection and evaluation of cost-reducing and performance-enhancing materials easier and faster earlier in your design cycle, speeding your time to market.