For every injection molded plastic part, there are a potentially limitless number of ways to design and manufacture it. Every mold engineer wants to find the way that produces the best results, whether functional or cosmetic or both, for the lowest cost. However, this can be incredibly difficult to do, whether you are designing a simple housing or a complex manifold.
One of the biggest problems with finding the “perfect” approach, is time. Most engineers are under a great deal of pressure due to schedules that have to accommodate all the realities of the shop floor and the supply chain. In other words, most engineers rely on expertise and experience to make critical choices about the part design, process, mold design, and part material they are creating.
They often think, if I’ve designed a similar part so many times, using the same trusted process, why change it? And because all of this happens very early in a project’s timeline, this effectively limits what you can be optimize as a project evolves.
Often times, “opening up” the design phase to more exploration reveals opportunities to reduce cycle time and improve efficiency. What’s more, it can also help boost profitability in ways that you had not even considered or simply assumed they were unavailable.
Autodesk Moldflow: Mold Injection
Injection molding has a long list of variables in play, and setting up a Design of Experiments (DOE) forces you to select the most important ones. For each one, such as wall thickness, you establish a midpoint, low point (-15%) and high point (+15%). The DOE helps determine how to find the most important relationships between variables without running every possible combination (which would be too time-consuming). Instead, the DOE narrows down the choices to a dozen tests, from which engineers can infer how best to manipulate these variables to achieve the desired goal.
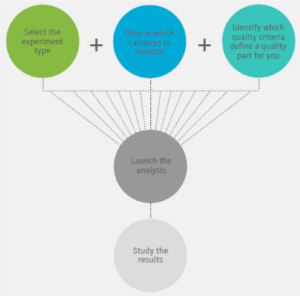
Autodesk Simulation Tools
The kind of exploration that mold engineers can utilize during a relatively short timeline is driven by the simulation software. Simulation tools can be used to test different “big decisions” quickly. The idea is to build confidence into your idea. That’s how you can predict what will happen and be reasonably certain it is a viable alternative to the default process.
Simulation tools like Autodesk Moldflow in Advanced Manufacturing toolset make it possible to mockup both traditional and conformal cooling systems for the sake of comparison. These two “sketches” will not resemble the final cooling system. That level of specificity comes during the design phase. However, a high-level comparison of both options can give you a baseline for how much faster your mold could run with conformal cooling.
Simulation tools also give you the advantage of parallel processing. If you have two choices for cooling and two choices for part material, you can simulate all four combinations to get an idea of which one will deliver the best outcome.
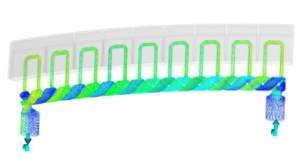
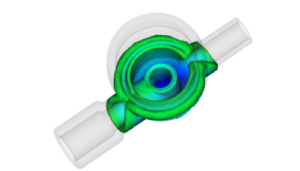
Over time, simulation helps you understand which approach will work best for a given project, or which aspect of a project would benefit from further exploration. This expertise gives mold injection engineers a distinct advantage for overcoming new part design challenges, process requirements, and material characteristics. Moreover, it can be beneficial in dealing with the familiar pressures of time, cost, and profitability.
Watch the Autodesk Virtual Academy video on Moldflow below!
————————————————————————-
About Nikhil Venkat
As an Application Engineer, Nikhil has been engaged in consulting and education services for the last three years, with a focus on simulation, CAD and data management. He earned a Master’s degree in Mechanical Engineering from the University of Florida, and Advanced Simulation and Product Design certifications from Autodesk.