Optimizing Generator Systems: From Design to Deployment
When it comes to generator systems, it’s essential to ensure that each generator is designed, properly sized and selected for its specific use case. .Whether a generator is needed for an industrial facility, a commercial building, or a residential property, selecting the right generator type and size is key to effective system design.Designers must overcome key challenges, apply advanced design solutions, and leverage modeling tools to create effective systems.
Challenges in Generator System Design
Designing a generator system that meets specific needs involves navigating two primary challenges:
- Sizing Requirements: Determining the correct size of the generator is essential to meet the input and load requirements. An undersized generator may lead to power shortages, equipment failures and costly downtime, while an oversized one can result in unnecessary costs and inefficiencies.
- Selecting the Appropriate Generator Type: With a wide variety of generator types available, selecting the one that best suits the application’s needs—whether it’s for continuous, standby, or prime power—requires a deep understanding of the application’s specific operational requirements and conditions.
Ansys White Paper
Electrothermal Mechanical Stress Reference Design Flow for Printed Circuit Boards and Electronic Packages
PCB simulation can be utilized for all electrical CAD (ECAD) types such as IC packages, touch panel displays, and glass and silicon interposers. The authors of this white paper followed this reference design flow for analyzing a PCB virtual prototype used in the consumer electronics industry. The design flow details nearly all aspects of the modeling technique from studying electrical connections in a schematic and setting up the PCB to analyzing the electrical, thermal and mechanical characteristics of the board — all using ANSYS tools. The multiphysics simulation yields power losses across the entire board and its objects, determines whether the integrated circuit (IC) and overall board temperatures lie within safe operating limits and predicts overall PCB reliability, taking into account all its components and heat sinks.
Download the white paper to learn more!
Solutions: Advanced Design and Modeling
To effectively address these challenges, engineers use advanced design and simulation tools that help optimize generator systems for their intended applications. Here’s how these solutions make a difference:
- Extensive Library of Machine Topologies: These tools offer a wide range of machine topologies—such as synchronous and asynchronous generators—allowing engineers to customize and model configurations that precisely match application needs.
- Full Parameterization: These design tools are fully parameterizable, enabling engineers to adjust and optimize every aspect of the generator’s design, from electrical to mechanical properties, ensuring the system is fine tuned for peak performance
- Comprehensive Evaluation: The tools support concept design and detailed evaluations of electromagnetic (EM), thermal, and noise, vibration, and harshness (NVH) performance, ensuring the generator is optimized for all aspects of its operation.
- Seamless Integration with FEA Tools: For more detailed analysis, designs can be easily exported into 2D or 3D Finite Element Analysis (FEA) tools. This allows for precise examination of the generator’s performance under various conditions.
- Model Creation for System-Level Simulation: The ability to create models that integrate into system-level simulation tools such as Twin Builder, Maxwell, RMxprt, and Motor-CAD ensures that the generator’s performance can be thoroughly validated within the context of the entire system.
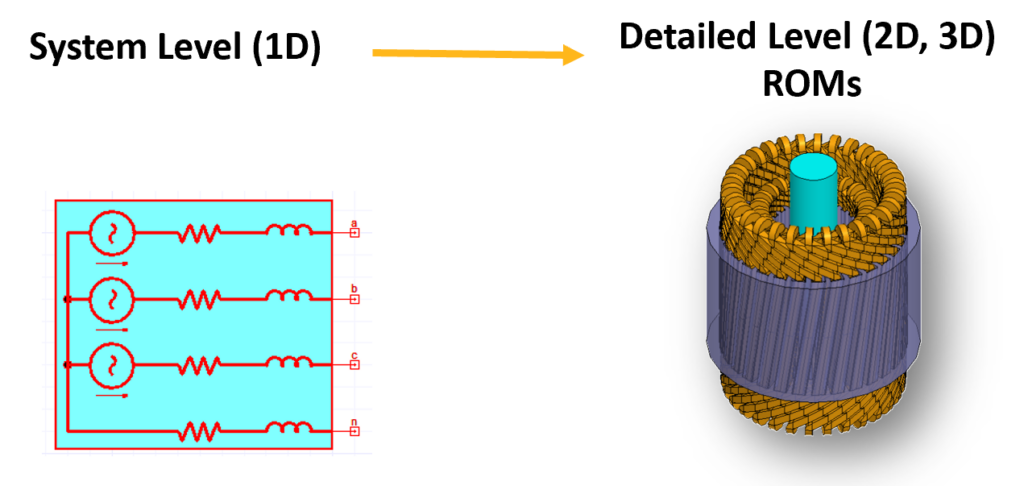
Benefits: A Systematic Approach to Validation
Employing these advanced design and modeling tools yields several key benefits:
- System Simulation Validation: Simulating generator performance within the entire system allows engineers to validate that all specifications are met, reducing the risk of system failures and improving overall reliability.
- Fault Mode and Effects Analysis: Understanding potential fault modes and their effects before they occur helps in designing more reliable and resilient generator systems.
- Energy Balance Validation: Validating the system’s energy balance ensures that the generator operates efficiently, with optimal energy distribution across the system.
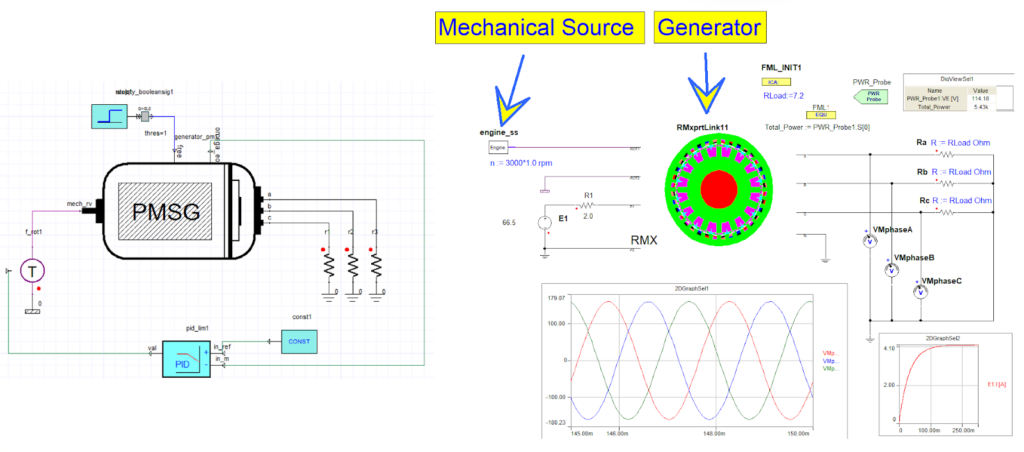
Precision in designing generator systems—ensuring the right size, type, and configuration—is crucial to achieving optimal performance and reliability.t. By utilizing advanced design and modeling tools, engineers can not only overcome the challenges of sizing and selection but also create robust systems that are validated and optimized for their specific applications. These solutions ensure that generator systems are not just fit for purpose but are also efficient, reliable, and ready to meet the demands of their intended environments.