Overview
Rapid and confident results for engineers
Ansys Mechanical empowers you to address intricate structural engineering challenges and enhance the speed and quality of your design decisions. The suite’s finite element analysis (FEA) solvers allow you to tailor and automate solutions for structural mechanics issues and parameterize them to evaluate various design scenarios. Ansys Mechanical is a versatile tool equipped with a comprehensive array of analysis capabilities.
- User-Friendly, Versatile Tool
- Integrated, Adaptive Platform
- Reliable, Accurate, Consistent Solver Technology
- Robust Nonlinear and Linear Solvers
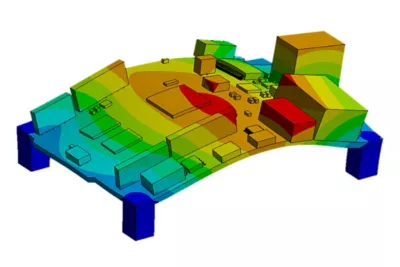
Product Specs
Ansys Mechanical provides a versatile environment with an extensive suite of analysis tools, ranging from geometry preparation to integrating additional physics for enhanced accuracy. The intuitive and adaptable user interface allows engineers of all experience levels to quickly and confidently get results.
What's New
July 2024 R2 release of Ansys Mechanical
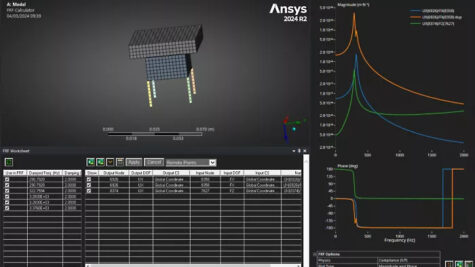
NVH Workflow Enhancements
The NVH Toolkit has been upgraded with new features, including a frequency response function (FRF) calculator, a transfer path analysis (TPA) calculator, and an XML converter for electromagnetic loads. The FRF calculator now supports stress and strain computations and integrates smoothly with data processing frameworks. Meanwhile, the TPA calculator enhancements allow for handling more complex data and offer better visualization capabilities.
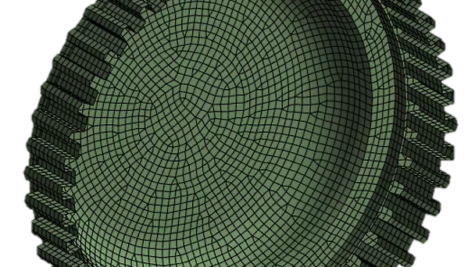
Expanded Simulation Capabilities
Introducing fluid penetration pressure load for simulations involving fluid-structure interaction and resource prediction, supporting harmonic response and nonlinear static structural analysis.
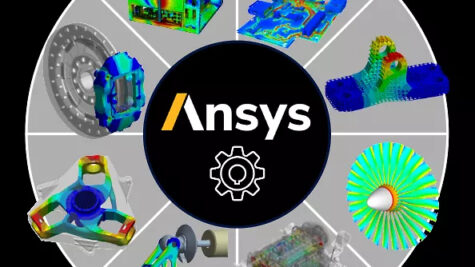
Additions for Interoperability
This release introduces the ability to import models from ABAQUS and LS-DYNA, along with enhanced data import functionality from Rocky, which automates the setup of convection and force loads.
Applications
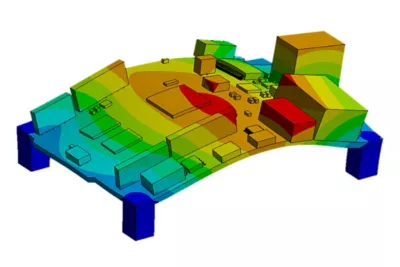
Electronics Reliability
Discover how Ansys integrated electronics reliability tools can assist you in addressing your most significant thermal, electrical, and mechanical reliability challenges.
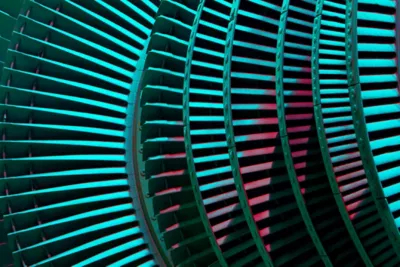
Turbomachinery
Ansys rotating machinery simulation enhances the design of fans, pumps, and compressors by boosting efficiency, safety, and durability.

Electric Motors
From concept design to detailed electromagnetics, thermal, and mechanical analysis, Ansys electric motor design software facilitates comprehensive analysis of electric motors.
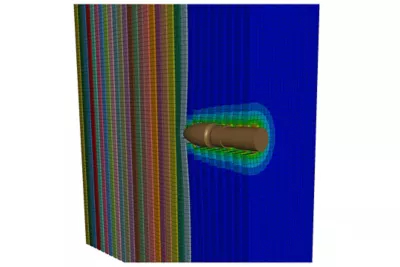
Battery Structural Reliability
Ansys provides simulation solutions for optimizing housing designs and reinforcements to ensure battery durability, reliability, and safety.

Meshing
Ansys offers high-performance, automated meshing software that generates the optimal mesh for FEA, CFD, and various multiphysics solutions.
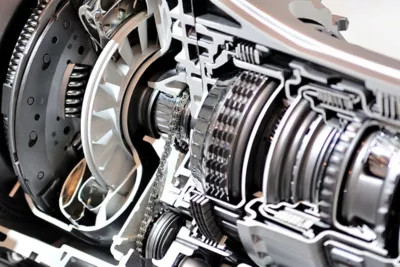
Rotating Machinery
Ansys rotating machinery simulation improves safety, efficiency, and durability by enhancing the design of fans, pumps, and compressors.
Capabilities
Instill quick confidence in preparing geometry using a wide array of analytical tools
Ansys Mechanical provides a unified platform utilizing finite element analysis (FEA) for structural analysis. This dynamic environment offers a full suite of analysis tools, from geometry preparation to integrating additional physics for enhanced accuracy. Its intuitive and customizable user interface allows engineers at all levels to quickly and confidently obtain results.
Ansys Workbench offers strong connectivity to commercial CAD tools, enabling easy design point updates with a simple click. It also features seamlessly integrated multiphysics capabilities, including fluid and electrical solvers.
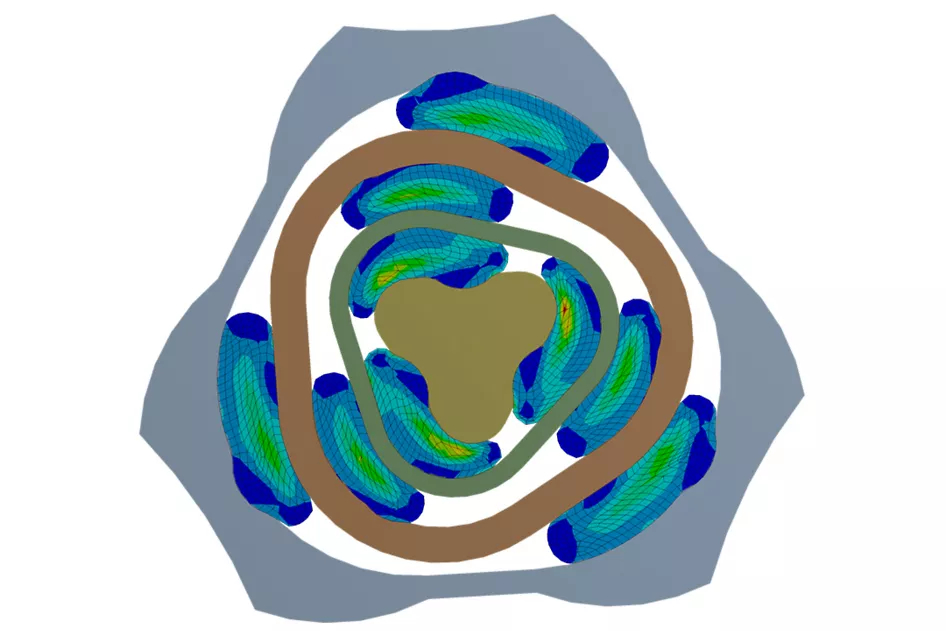
Key Features
Experience dynamic analysis and embrace advanced solver options across a variety of materials and functions
- Linear Dynamics
- Nonlinearities
- Thermal Analysis
- Materials
- Composites
- Hydrodynamics
- Fluid-Structure Interaction
- Customization and Scripting
- Solve Management
- High Performance Computing
Linear Dynamics
Ansys Mechanical addresses all your linear dynamic analysis requirements, including modal, harmonic, spectrum response, and random vibration with pre-stress, complemented by advanced solver options for quick solutions.
Perform acoustics simulations to comprehend the vibroacoustic behavior of systems, with or without structural pre-loading. Including pre-loading enhances fidelity, allowing for the simulation of self-weighted, bolted assemblies, or even squealing brakes.
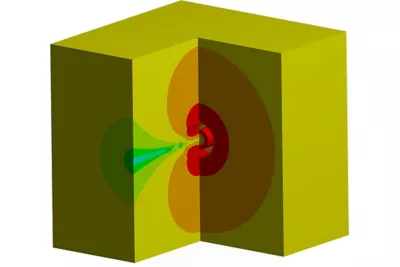
Nonlinearities
Expanding beyond linear, elastic materials, Ansys Mechanical enables the simulation of materials undergoing plastic or hyperelastic deformation, such as rubber and neoprene. Nonlinear simulation also considers contact and significant deflection of parts moving relative to each other, with or without friction.
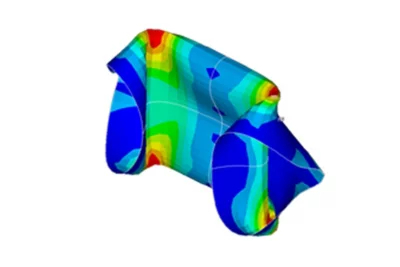
Contact
Ansys Mechanical offers an extensive range of contact capabilities to account for interactions between multiple parts.
It can simulate everything from bonded contact, treating joints between parts as if they are glued or welded together, to contact interfaces that allow parts to move apart and together, with or without frictional effects. Proper contact simulation enables accurate modeling of load path changes when parts deform, providing confidence in predicting real-world assembly behavior.
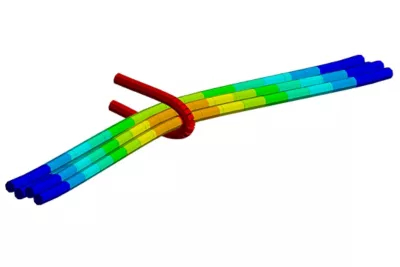
Structural Optimization
Ansys Mechanical features parametric, shape (mesh morphing), and topology optimization. Any model within Ansys Mechanical can be utilized for parametric optimization.
The shape and topology optimization capabilities enable the creation of efficient geometries, which can be exported back to CAD for production or further simulation. This technology is particularly beneficial for additive manufacturing, lightweighting, and robust design.
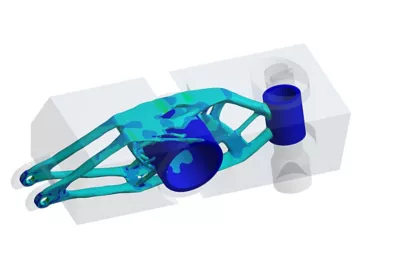
Thermal Analysis
Simulating heat conduction, convection, and radiation across assemblies allows you to predict component temperatures, which can then be analyzed for induced stresses and deformations.
With Ansys Mechanical, you can import power losses or calculated temperatures from other analysis systems or files, allowing CFD or electromagnetic simulations to serve as the basis for thermal analysis. Additionally, it can account for fluid flow through pipes and heat generated from friction between parts. These capabilities lead to more accurate simulations and improved results.
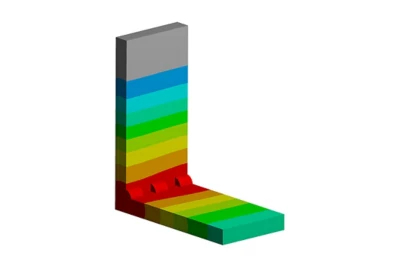
Materials
A range of material models covering everything from hyperelastics, shape-memory alloys, soils, concrete, plastic and metallic structures can be accurately modeled in Mechanical.
You can also add user-defined material models, if needed. Granta Materials Data for Simulation provides instant, clickable access to the materials property data you need, eliminating data search time and input errors. Material Designer can easily create representative volume elements (RVE’s) based around lattice, fiber, weave or user-created geometries to facilitate multiscale modeling of complex material structures.
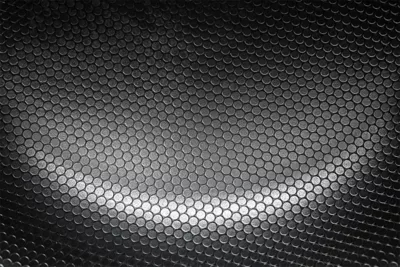
Composites
Ansys Mechanical offers capabilities for modeling short fiber composites, utilizing data from upstream manufacturing simulation tools.
It also supports modeling layered composites through its connection with Ansys PrepPost (ACP) and short fiber composites via upstream manufacturing simulation tools and material behavior obtained from Material Designer, Ansys' tool for multiscale homogenization of material microstructures.
You can generate composite models for implicit and explicit structural, thermal, and fluid simulations. Ansys Composite PrepPost (ACP) is a dedicated tool for modeling composite layups and failure analysis. ACP provides efficient layup and best-in-class solid element modeling capabilities and a versatile platform for exchanging model information. It supports the vendor-independent HDF5 composite CAE file format for communication with third-party tools, many of which are dedicated to composites manufacturing. Additionally, Ansys Composite Cure Simulation (ACCS) extends Ansys Mechanical to simulate the curing process during manufacturing, predicting residual stresses and process-induced distortions to facilitate compensation analyses.
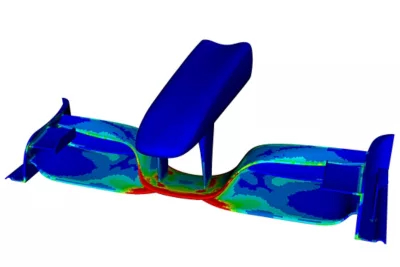
Hydrodynamics (Ansys Aqwa)
Ansys meets the majority of analysis requirements for hydrodynamic assessment of various offshore and marine structures.
These structures include SPARs, FPSOs, semi-submersibles, tension leg platforms, ships, renewable energy devices, and breakwaters. Ansys Aqwa has been widely used in the oil and gas, renewable energy, and general engineering sectors to model the installation and utilization of equipment in open water, harbors, or sheltered locations.
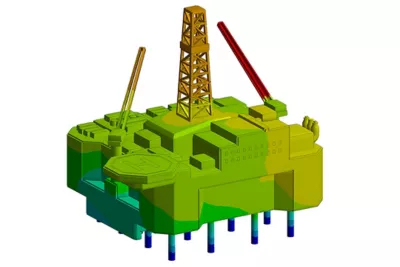
Fluid-Structure Interaction
Accurately predict interactions between fluids and solids from pressure and/or thermal loads with Ansys. As fluid-structure interaction becomes more complex and requires detailed evaluation, Ansys provides automated, easy-to-use solutions for both one-way and two-way coupling.
In one-way coupling, the initial CFD or Ansys Mechanical simulation is solved, and the data is automatically transferred and mapped to the other system. In two-way coupling simulations, the fluid and structural simulations are set up and solved concurrently, with data being automatically transferred between the two solvers to achieve robust and accurate results.
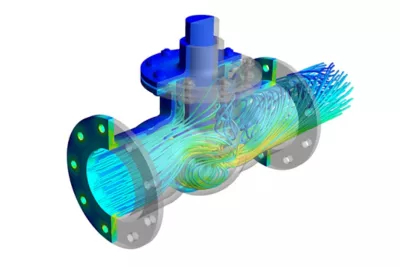
Customization and Scripting
The fastest and simplest way to tailor your simulation workflows is through customization within Ansys Mechanical. This allows you to automate repetitive tasks or specific workflows and share them among users.
With journaling and scripting capabilities, you can quickly develop and easily teach new scripts.
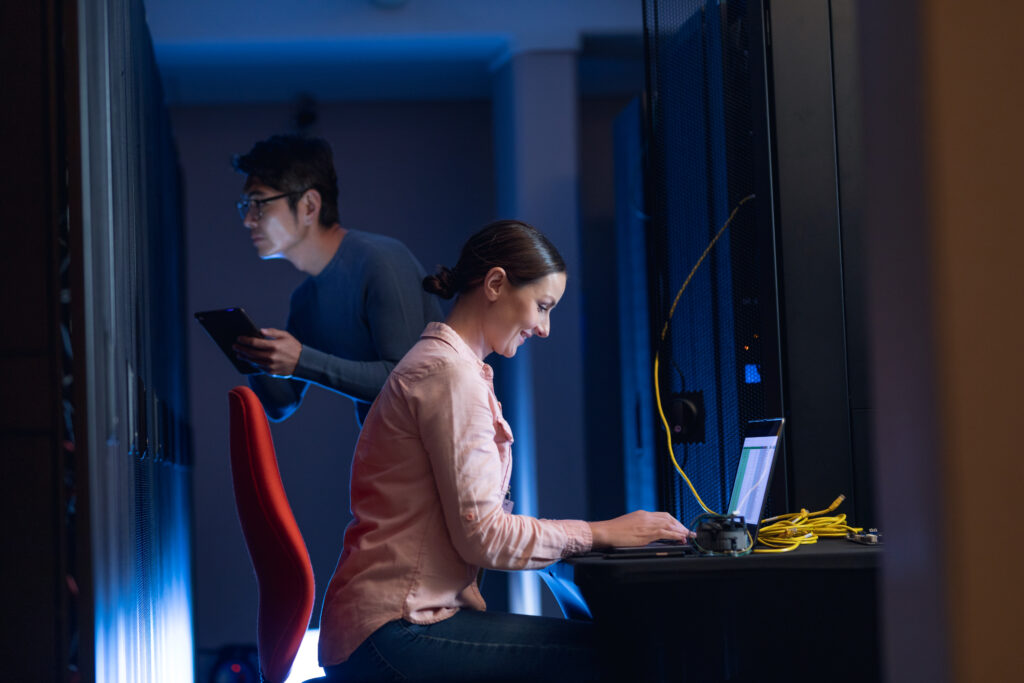
Ready to start working with Ansys Mechanical?
Resources
Are My Simulation Results Valid?
Electrothermal Mechanical Stress Reference Design Flow for Printed Circuit Boards and Electronic Packages
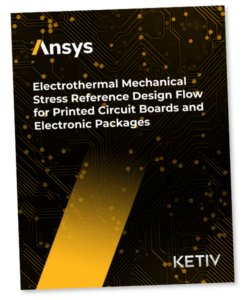