KETIV Blog
Stay up-to-date with the latest technologies, best practices, processes, and industry advances for the manufacturing community.
Filter by topic:
Search for something:
string(85) "https://ketiv.com/wp-content/uploads/2025/07/ansys-thermal-desktop-banner-475x267.jpg"
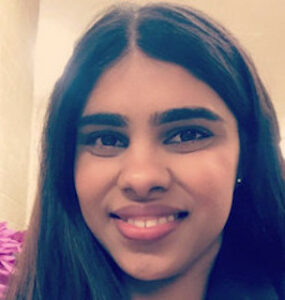
Ansys Thermal Desktop Installation Guide: Step-by-Step
This guide provides a comprehensive, step-by-step overview of the Ansys Thermal Desktop installation process, ensuring you have all prerequisites in place and avoid common pitfalls. Whether you’re new to Ansys products or a seasoned simulation engineer, follow this guide to get up and running quickly.
See the full story
string(161) "https://ketiv.com/wp-content/uploads/2025/06/ketivmarketing_integration_between_CAD_design_and_finite_elemen_217646e6-e386-4df2-9b17-28def772b153_png-475x267.jpg"
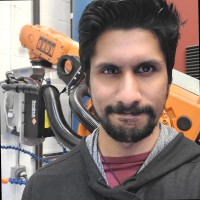
How to Sync Inventor to Ansys Using Live Parameters
Tired of redoing your work every time you tweak a CAD model in the middle of a simulation? You’re not alone. This guide walks you through how to set up true live parameter sync and bi-directional tracking between Autodesk Inventor and Ansys, eliminating repetitive work and boosting your simulation productivity.
See the full story
string(161) "https://ketiv.com/wp-content/uploads/2025/04/ketivmarketing_a_busy_design_engineer_getting_tons_done_because_9727d074-e6f3-4729-9a2e-4f94b06ef4d1_png-475x267.jpg"
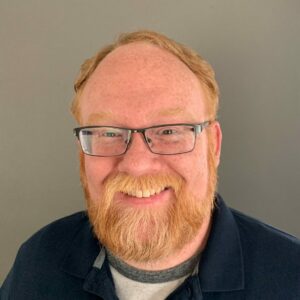
Getting Started with Autodesk Inventor Automation: iLogic vs. Add-Ins
Learn how to dramatically reduce design time in Autodesk Inventor using automation. Explore the benefits of iLogic and custom add-ins, and find out which approach fits your product design needs.
See the full story
string(83) "https://ketiv.com/wp-content/uploads/2021/04/what-s-new-in-vault-2022-6-475x267.png"
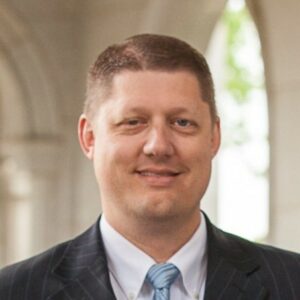
How To Configure Inventor Content Center Libraries Using Autodesk Vault
If you’re still relying on local Content Center libraries in Autodesk Inventor, you may be missing out on the true power of data management with Vault.
See the full story
string(106) "https://ketiv.com/wp-content/uploads/2025/05/an_engineer_dealing_with_complex_engineering_ECOs-475x267.jpg"
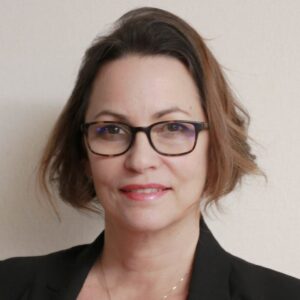
How to Use ECOs in Autodesk Vault ECOs—With or Without Items
If you’re managing design changes in Autodesk Vault, you might be wondering: Can Engineering Change Orders (ECOs) work in a Vault that’s not item-based? The short answer is yes—and there’s more flexibility than you might think.
See the full story
string(116) "https://ketiv.com/wp-content/uploads/2025/05/Screenshot-Integrate-CPQ-with-AutoCAD-and-Autodesk-Inventor-475x267.jpg"
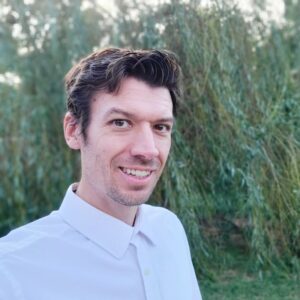
Streamlining Custom Product Design with Automated CAD
Discover how integrating product configuration with Autodesk Inventor helps manufacturers automate custom product design, eliminate repetitive CAD work, and accelerate sales-to-production workflows.
See the full story
string(78) "https://ketiv.com/wp-content/uploads/2025/03/Modern-Mfg-Buyer-Hero-475x267.png"
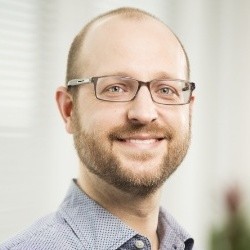
How The Manufacturing Sales Process Has Evolved
Beyond simply improving products, manufacturers must focus on refining the buying experience across the awareness, consideration, and decision-making stages.
See the full story
string(72) "https://ketiv.com/wp-content/uploads/2024/10/Ansys-Brand-BG-475x267.jpeg"
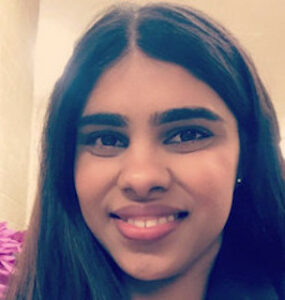
Ansys 2025 R1 Release Highlights – New Features in 3D Design, Simulation & Safety
Ansys 2025 R1 is the first major release of the year, delivering sweeping upgrades across the simulation portfolio. From 3D design and electronics to fluids, optics, and materials, this release boosts simulation speed, accuracy, and collaboration.
See the full story
string(161) "https://ketiv.com/wp-content/uploads/2025/01/ketivmarketing_illustration_of_a_cloud_hosted_product_data_mana_0966ea93-b826-4c8b-b13f-5aaefe2de57b_png-475x267.jpg"
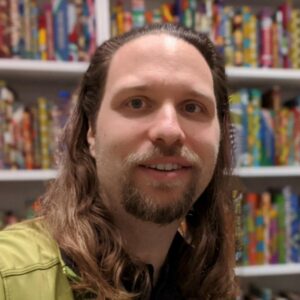
Cloud-Hosted PDM: What’s Stopping You?
Ever found yourself on the fence about moving your Autodesk Vault PDM system off that old server in the back room? You’re not alone. Many teams hesitate—whether it’s security concerns, costs, or just the comfort of sticking to what they know. In this post, we’ll explore what’s holding you back and why a cloud-hosted Vault setup could streamline your workflow, letting you focus on engineering instead of server upkeep. Let’s dive in.
See the full story
string(161) "https://ketiv.com/wp-content/uploads/2025/01/ketivmarketing_An_isometric_illustration_of_a_cluttered_workspa_c196d8cf-0dfb-4250-9552-0db741896c48_png-475x267.jpg"
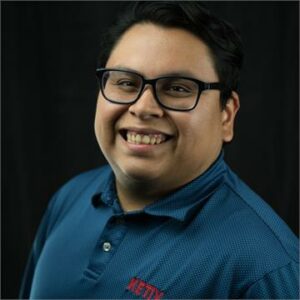
Outgrowing Shared Drives: Your Path to Smarter Engineering Data Management
Managing CAD files on shared drives can lead to broken links, lost data, and version conflicts. Without proper controls, sensitive data and productivity are at risk. Jump into the article to learn why shared drives may not be the right answer for PDM.
See the full story
string(90) "https://ketiv.com/wp-content/uploads/2024/12/discovery-r2-2024-borderline-bolt-475x267.jpg"
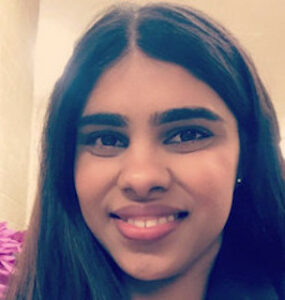
How Can You Take 3D Design Further with Interactive Simulation?
As an engineer, you're intimately familiar with the pressures of modern design cycles. The relentless push for innovation under tight deadlines is a constant challenge. You rely on tools like Autodesk for modeling, having honed your workflow over years of experience. But what if there was a way to take that investment further—moving beyond static 3D design to a process that combines modeling with interactive simulation? Traditional simulation tools often feel overwhelming, with steep learning curves and intricate workflows—the last thing you need when juggling multiple projects. But imagine a solution as intuitive and seamless as your modeling process, empowering you to design smarter and faster.
See the full story
string(161) "https://ketiv.com/wp-content/uploads/2024/11/ketivmarketing_A_futuristic_data_center_surrounded_by_glowing_l_0bd15ae2-c6b3-4e9f-8d61-e69f48e21c55_png-475x267.jpg"
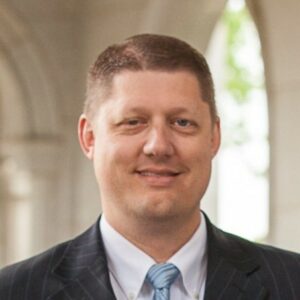
7 Lessons Learned: Keeping Engineering Data Healthy and Safe
Managing engineering data with Autodesk Vault can transform your processes, but only if it’s implemented and maintained correctly. Without proper management, your Vault environment can become chaotic, leading to inefficiencies, data loss, or costly downtime. Here are seven key lessons learned from real-world scenarios to help you optimize your Vault environment and avoid common pitfalls.
See the full story
string(81) "https://ketiv.com/wp-content/uploads/2024/10/green_floating_geometric-475x267.jpg"
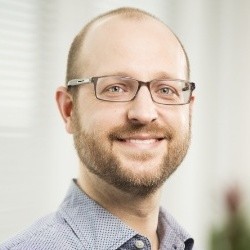
Product Life Cycle Management: A Catalyst for Business Transformation
We recently received an excellent white paper from Harvard Business Review and Autodesk, "Product Life Cycle Management: A Catalyst for Business Transformation". I had the opportunity to share the white paper with John Kuta at KETIV, and then get his insights on how this PLM story aligns with his extensive experience in value engineering in our field. Here’s how the conversation unfolded.
See the full story
string(119) "https://ketiv.com/wp-content/uploads/2024/03/ketivmarketing_Integration_Considerations_and_Data_Preparation-475x267.jpg"
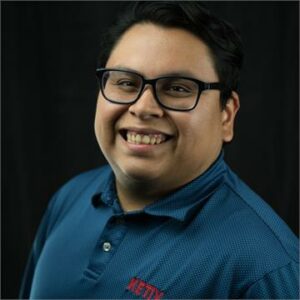
Vault It or Lose It: 13 Reasons to Get Your Data in Order with Autodesk Vault
Ever feel like your design data is scattered across too many places, causing more frustration than progress? Autodesk Vault is built to simplify the chaos, helping engineers, designers, and teams stay in sync and move projects forward without the usual hiccups. Here’s a breakdown of how Vault streamlines workflows, prevents costly errors, and keeps everyone on the same page.
See the full story
string(67) "https://ketiv.com/wp-content/uploads/2023/01/tablet-CPQ-475x267.jpg"
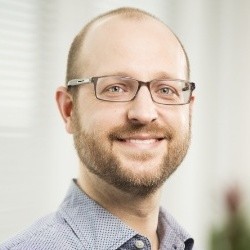
CPQ Software Selection: What to Consider When You Want to Re-Configure
As manufacturing companies grow and their product offerings become more complex, many find that their homegrown or legacy Configure, Price and Quote (CPQ) tools can no longer keep up.
See the full story
Quick tech tips
AutoCAD Electrical Bill of Materials Report Says “No Data to Display”
Discover the solution to address the "No Data to Display" issue in the AutoCAD Electrical Bill of Materials Report. This report specifically showcases components that have been assigned catalog data. If you encounter the absence of data, follow these steps to resolve the issue...
Check out the tech tip
How to Make a Previous File Version the Latest Version in Vault Professional
Learn how to make a previous file version, the latest version of Vault Professional. Get the steps and watch the video here.
Check out the tech tip